01
Can You Explain These Concepts About Welding?
2024-09-21
What is weld, weld metal, deposited metal?
The weld is the connection formed between two workpieces after welding. The metal that makes up the weld is called weld metal, which is generally formed by the fusion and solidification of molten base metal and filler metal.
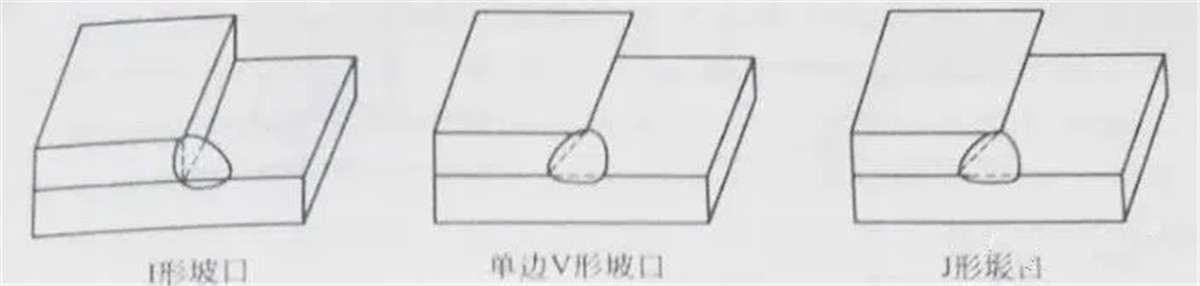
Common lap joint combination forms
The part of the weld metal formed by completely melting the filler metal is called deposited metal, also known as the full weld metal.
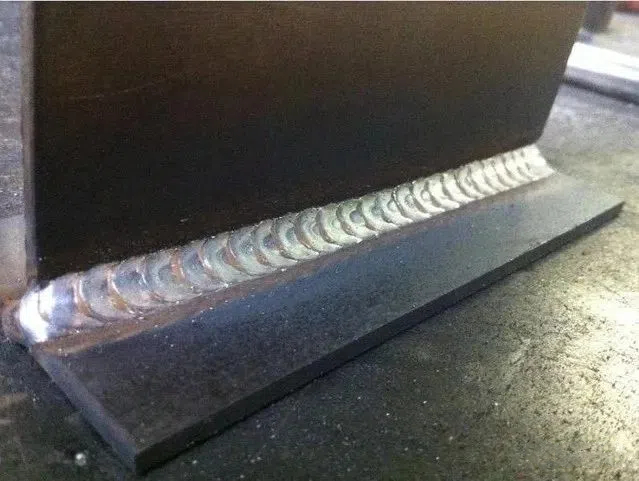
What is filler metal?
The general term for the metal used to fill the weld during welding, also known as filler material, including welding wire, welding rod and filler metal.
What are weld surface and weld back side?
The weld surface located on the welding surface of the weldment is called the weld surface. The surface of the weld located behind the welding surface is called the back side of the weld.
What are weld axis, weld toe and weld root?
The line along the length of the weld connecting the geometric centers of the weld cross-sections is called the weld axis. The connection between the weld surface and the base metal is called the weld toe, see figure.
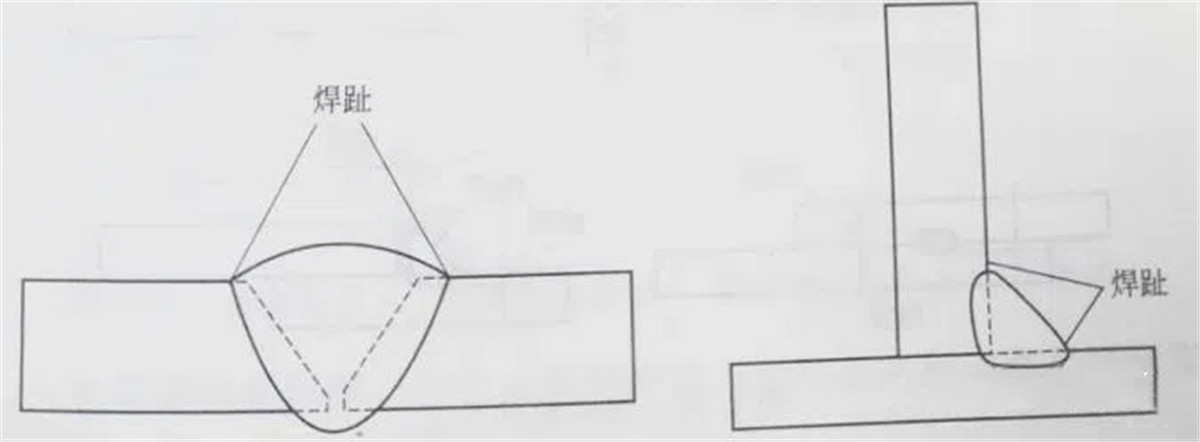
The intersection between the bottom of the weld and the base metal is called the weld root, also known as the weld root, as shown in the figure:
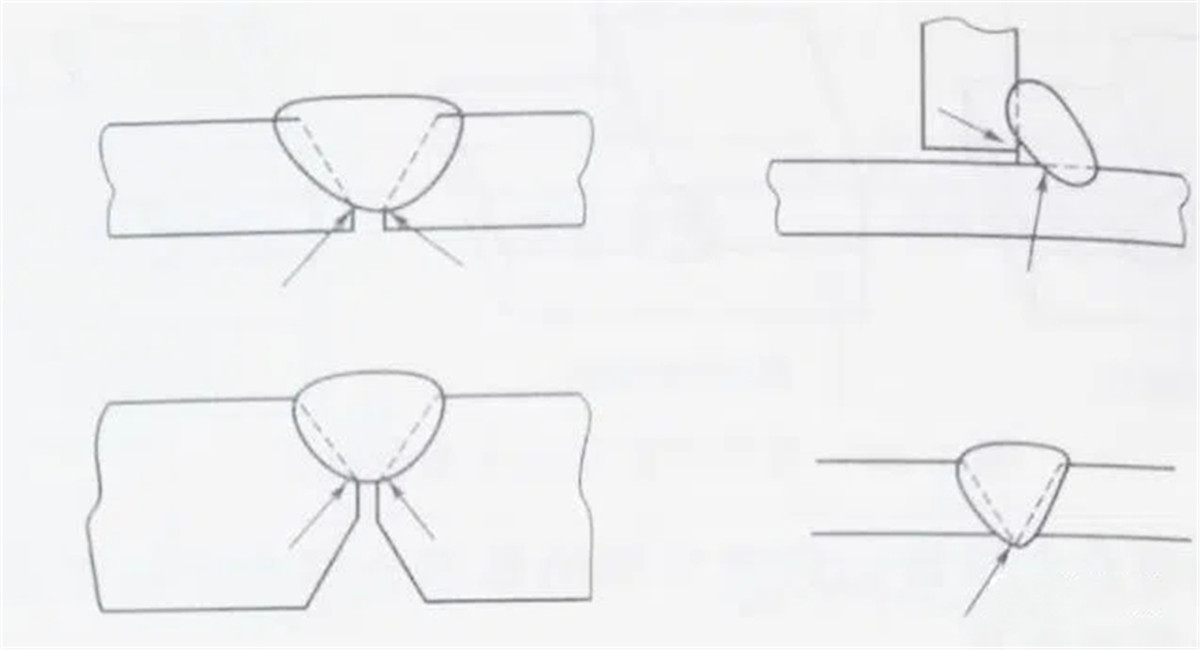
What are melt width, melt depth and reinforcement?
On the cross-section of the weld, the distance between the two weld toes is called the weld width, also known as the weld width, as shown in the figure:
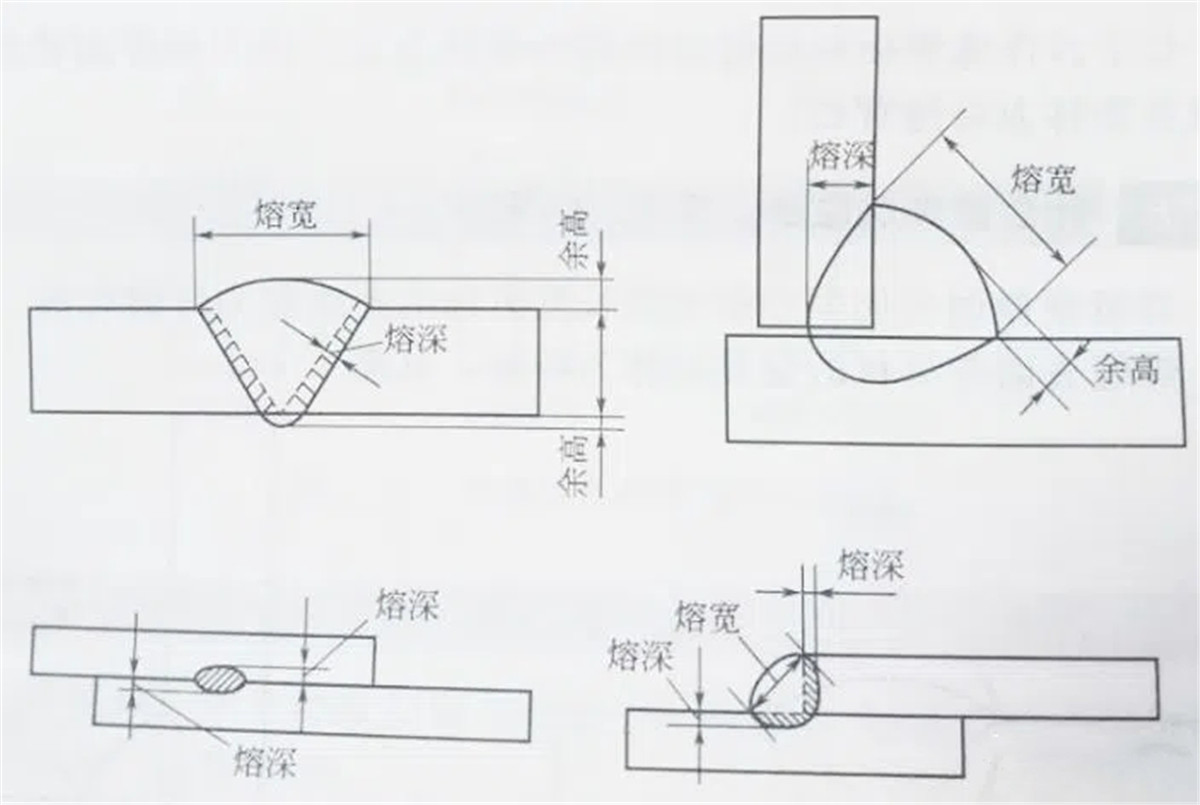
Weld shape and size
On the cross-section of the weld, the melting depth of the base metal is called penetration, as shown in the figure above; penetration directly determines the bonding strength of the weld and the base metal, and also determines the load-bearing capacity of the weld to a large extent.
The maximum height of the part of the weld beyond the surface of the workpiece is called reinforcement, which is the distance from the vertex of the weld to the line connecting the two weld toes. See picture above. For fillet welds, reinforcement is also called crowning. The strengthening of the weld increases the cross-sectional area of the weld and improves the static load carrying capacity. However, too high a height will cause stress concentration at the weld toe and reduce the ability of the weld to withstand dynamic loads. For weldments subject to dynamic loads or fatigue, the reinforcement ribs of butt welds should be ground flat, and the reinforcement ribs of fillet welds should be ground into a concave shape.
The ratio of melt width to reinforcement (B/a) is called the reinforcement coefficient. For butt welds, it should generally be 4~8 (or steel bars should be 0~3mm).
What is the weld thickness h and the calculated thickness h of the weld?
In the cross-section of the weld, the distance from the root of the weld to the line connecting the two weld toes is called the weld thickness, represented by h, as shown in the figure.
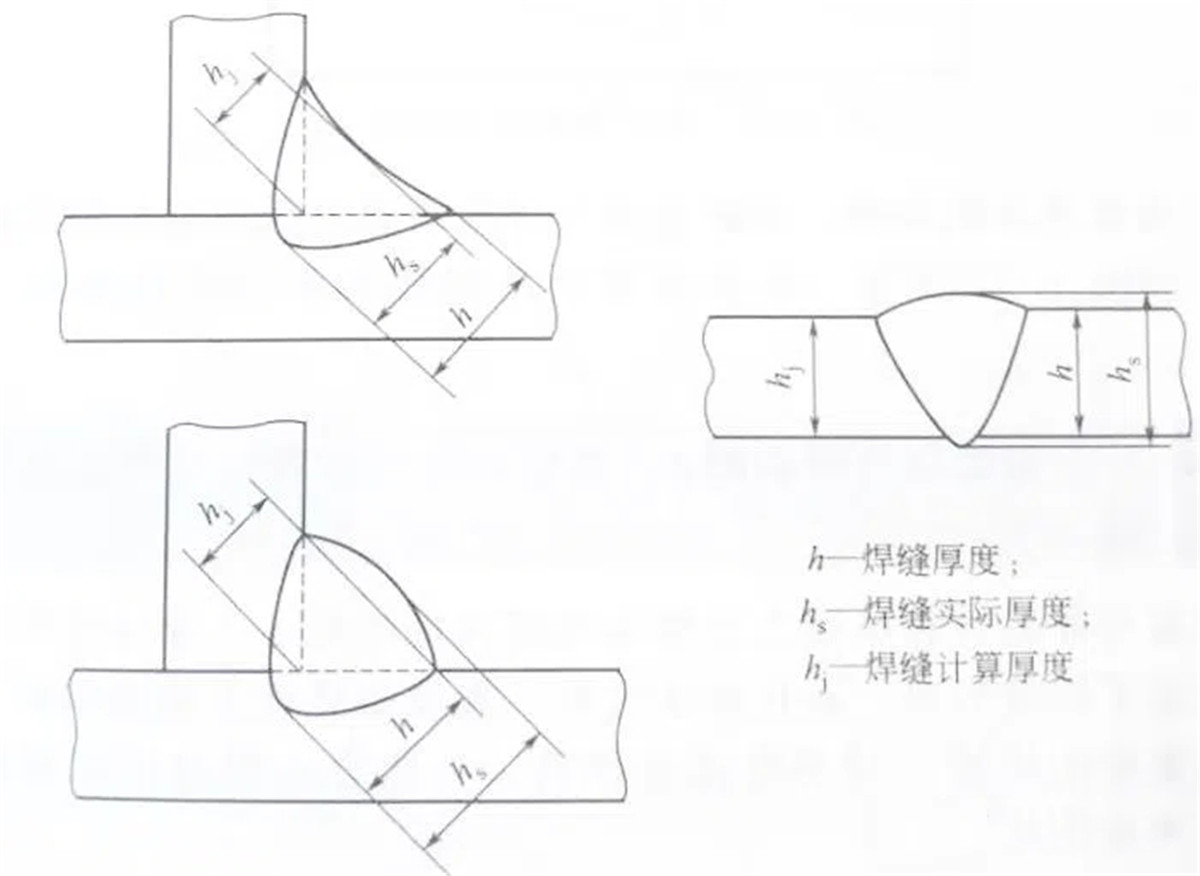
Schematic diagram of weld thickness h, actual weld thickness hs, and calculated weld thickness hj
In the cross-section of the weld, the maximum distance from the root of the weld to the surface of the weld is called the actual thickness of the weld, expressed by hs. The calculated butt weld thickness hj is equal to the weld thickness. For fillet welds, the calculated thickness is equal to the distance from the intersection of the inner surfaces of the two workpieces in the cross-section of the weld to the line connecting the two weld toes;
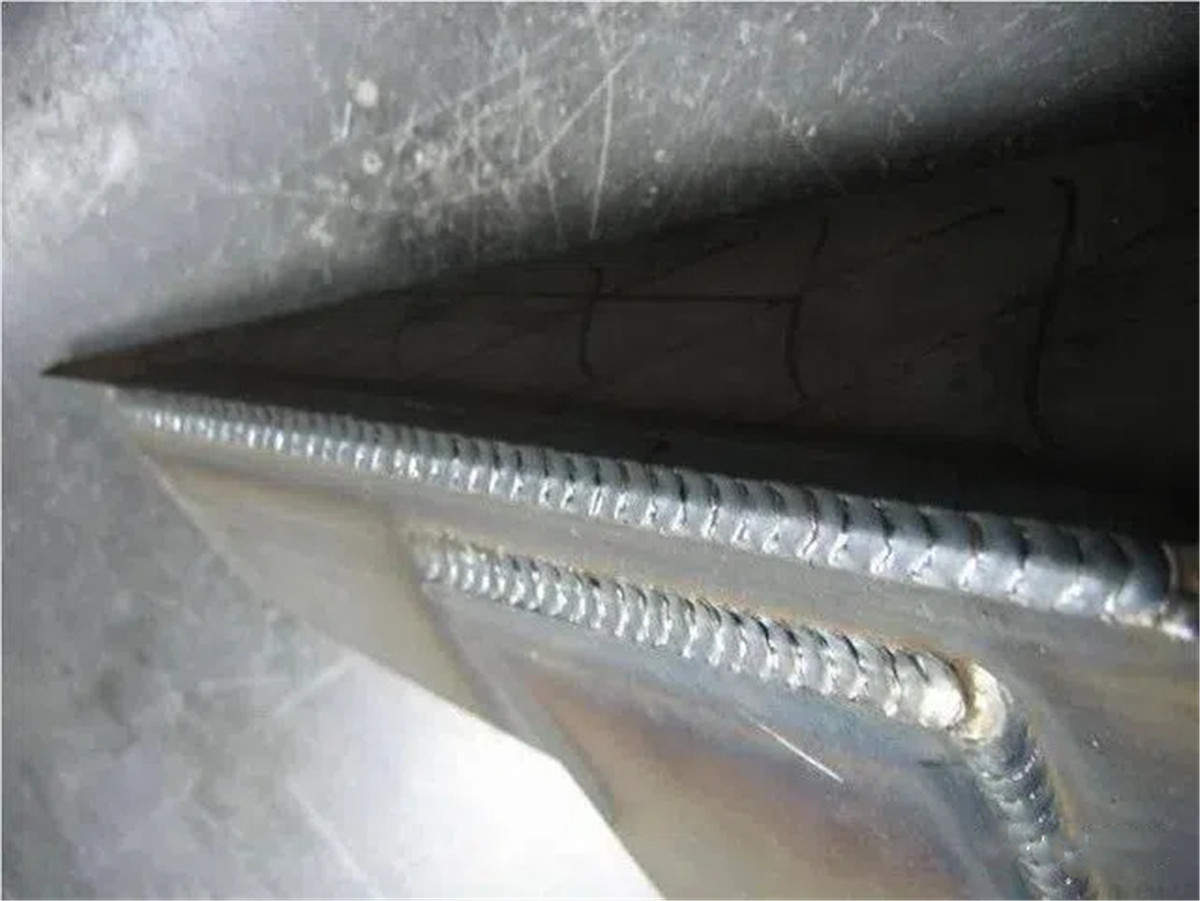
What are solder legs and concavity?
In the cross-section of a fillet weld, the distance from the weld toe of one weldment to the original surface of the other weldment is called the weld leg, as shown in the figure. The size of the welding leg determines to a large extent the bonding strength between the weldment and the weld, thereby determining the connection strength of the weld. It is the most important parameter of fillet welds.
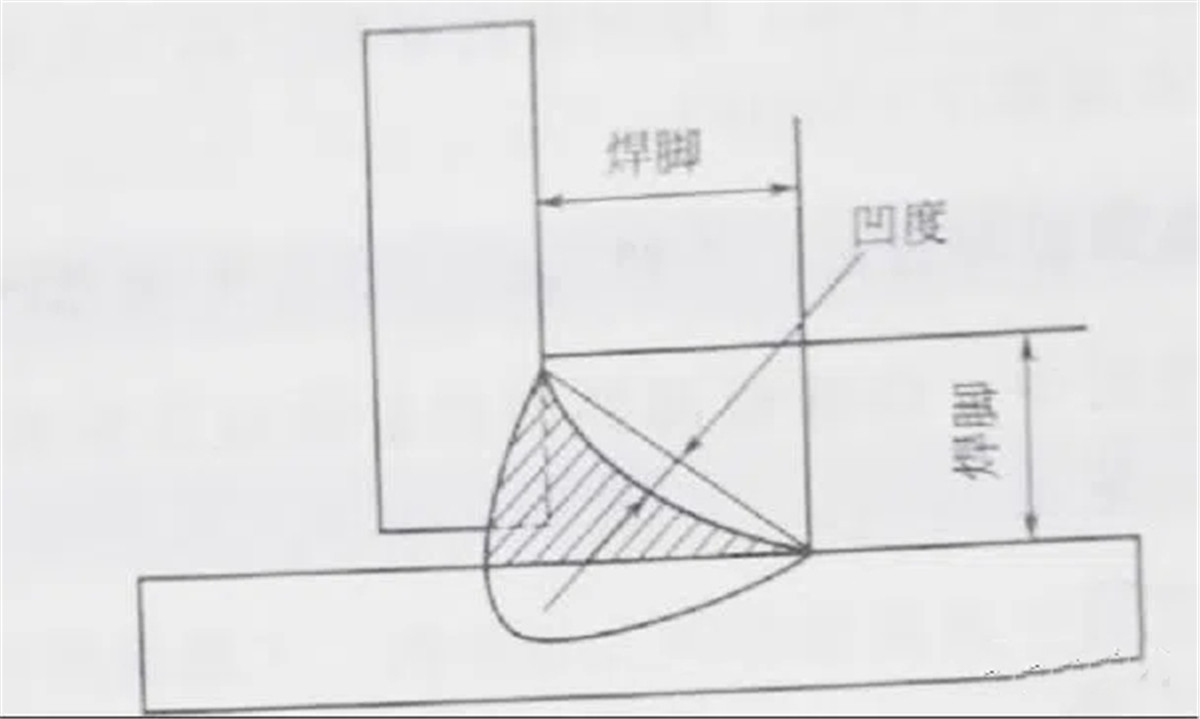
Fillet weld leg and concavity
In the cross-section of a concave angle weld, the maximum distance between the weld toe line and the weld surface is called concavity, as shown in the figure. Fillet welds subjected to dynamic loads usually require grinding to a certain concavity.
What is the weld forming coefficient φ?
The ratio of the melt width to the calculated thickness of the weld is called the weld forming coefficient φ. The weld forming coefficient not only determines the weld shape, but also has an important influence on pores, crack sensitivity and molten pool crystallization conditions. For arc welds, the weld forming coefficient is generally required to be greater than 1. The influence of weld forming coefficient on weld quality is as follows. ①The smaller the impact on stomatal sensitivity φ, the greater the stomatal sensitivity. ②Influence the crystallization direction. When φ<1, it crystallizes toward the center; when φ>1, it crystallizes upward, as shown in the figure. ③Influence on central segregation. If φ is too small, segregation will occur, and in severe cases, thermal cracking may occur.
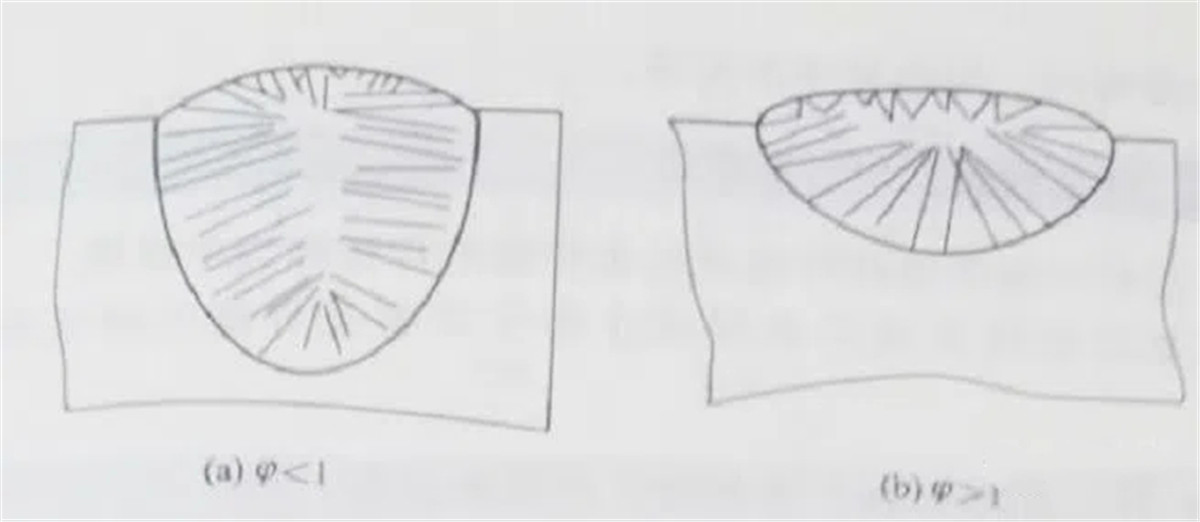
Effect of weld forming coefficient on crystallization direction of molten pool
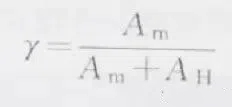
What is the fusion ratio? How to adjust the blending ratio?
On the cross-section of the weld, the ratio of the area of the base metal in the weld to the area of the entire weld is called the fusion ratio, which can be calculated by the following formula:
Am and AH see picture

Generally speaking, the properties of the wire metal are better than those of the corresponding base metal, so the composition and properties of the weld can be improved by adjusting the fusion ratio. Adjustment of the fusion ratio can be easily achieved by changing groove and gap dimensions.